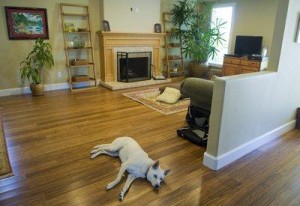
The dog Kaia finds a spot for a nap on the stranded bamboo floors in this remodeled green home. Bamboo is not a wood, it is a grass, and it is fast-growing, but at least as strong as some slow-growth woods. (Leonard Ortiz/Orange County Register/MCT) ( LEONARD ORTIZ )
Whether framing a new addition, building a deck or making a piece of furniture, wood is often the go-to material. Lumber, plywood and other products made with sustainably harvested wood are widely available and relatively inexpensive. However, there are environmental costs and structural drawbacks to many traditional wood products. Plenty of creative alternatives are available. Here is a sampling of wood alternatives, most with some environmental advantages, for home construction and remodeling projects.
1. Hemp
Hemp is a fast-growing and sustainable crop that generates more construction-grade fiber per acre than most trees and other crops. It can be used in place of lumber and a wide range of other materials. For example, Washington State University researchers found hemp-based medium-density fiberboard to be twice as strong as wood.
2. Bamboo
Bamboo is often considered a wood, but this grass is really a wood alternative. It has been called the world’s most useful plant (though hemp advocates might argue otherwise). Bamboo is fast-growing but at least as strong as some slow-growth woods. It is a very trendy flooring option. It is also used in furniture and a wide variety of other construction materials.
3. Wood composites
As the name suggests, composite materials combine wood with recycled plastics or other components. As compared to lumber, composites are a more sustainable way to use trees. For example, composite deck boards can be made with scrap wood fiber leftover from cutting solid hardwood deck boards. Composite decks and other products also have other advantages over hardwood. They require virtually no finishing, staining or maintenance, and are very durable.
4. Plastic wood
Another growing segment of the deck market is basically the plastic — recycled or not — of composites without any wood fibers. Like composite decking, plastic wood requires no maintenance. Of course, it’s hard to make plastic look exactly like wood, so it’s not a perfect aesthetic substitute. However, in many other ways, composites and plastic wood are good hardwood alternatives.
5. Soy
No, you can’t build walls out of tofu, but soy is another immensely useful plant that is used for insulation, carpet backing, paint strippers and more. While soy fibers may not be a substitute for wood, soy can make traditional wood products safer. Soy-based chemicals can replace the potentially dangerous formaldehyde, glues and other solvents.
6. Cork
Cork is made with bark rather than the core of a tree. That means it re-grows faster and is more sustainable in some ways than many traditional wood products. It is a popular flooring material, and is growing into other areas of construction and remodeling.
7. Cardboard
Cardboard construction isn’t just for kids. A couple of plywood substitutes on the market are made primarily with recycled cardboard.
8. Newspaper
Similarly, recycled newspaper is being used to create fiberboard products for roof decking and much more. For example, Homasote is a New Jersey company that claims to recycle up to 250 tons of newspaper each day into construction materials.
9. Nutshells
Maderon is a recyclable Spanish furniture-building material made primarily of crushed almond, hazelnut and walnut shells. The shells are ground into a paste, then mixed with resin and molded into chairs and other furniture.
10. Straw
Look closely at plywood. The fibers look a lot like straw, so it’s no stretch to imagine particleboard from varieties of straw, including wheat, oat and flax straw. All these are available and useful alternatives to traditional pressed-wood products.
Source: MercuryNews.com