By Mark Mizrahi | Are you are planning to put up a new “green” building, or retrofit an existing building with new green technology? Make your life easier and your project greener by considering the most efficient heating and cooling technology available today: geothermal heat pumps (GHP).
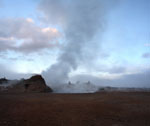
For the average commercial building in the US, 50 percent or more of the energy use will be for air conditioning, heating and ventilation. The equipment, operations and management of your HVAC systems are going to be a huge long-term cost that will significantly affect the value of the building for decades. GHP delivers the most long-term bang for the buck that you will find anywhere. GHP is also a tried and true technology; it’s been used in this country for more than half a century. With the new materials, technology, and construction processes available today, GHP is extremely reliable, damage resistant, efficient, and cost competitive.
The US Department of Energy estimates that GHP systems can range from 300 to 600 percent efficient. In other words, for every unit of energy you put into the system, you will get the equivalent of three to six units of energy back. Nothing else comes close.
That means you will use less electricity, and by extension less natural gas or coal, depending on where your electric utility gets its power. If you are going to use GHP to make hot water, you will reduce your gas and/or electric use even further. And if you are thinking of an HVAC system that uses an evaporative cooling system with cooling towers, you can virtually eliminate water used for cooling.
In the US our buildings are responsible for 39% of primary energy consumption and an equivalent 39% of all greenhouse gases. You can take a serious bite out of your carbon footprint by using GHP.
We should clarify that GHPs are not the same as “Geothermal Energy,” or “Big Geo”, which uses very hot rocks deep in the earth to create steam, which runs turbines that generate electricity. GHP simply uses the earth as a heat sink to either store or release heat when it’s needed. By moving water through high-strength underground pipes, and connecting those pipes to a highly efficient heat pump inside your building, heat is transferred into or out of your building as you choose.
Geothermal heat pumps are ready today to effectively fight climate change, reduce air pollution and increase energy efficiency, according to both the U.S. Department of Energy and the U.S. Environmental Protection Agency
GHP systems use the moderate and stable temperature of the earth from about 200 feet to 500 feet below the surface as a heat sink. The earth is capable of storing or releasing large amounts of energy that can then be used to heat or cool a building. Conventional HVAC systems work with the extreme temperatures of the outside air, so they have to do much more work to get the same amount of heating or cooling.
GHP systems use the moderate temperature of the water flowing through an underground heat exchanger, decreasing energy use as much as 70% compared to a traditional HVAC system. Depending on the region, the water temperature (heat transfer medium) will be in the range of 45-70˚ F.
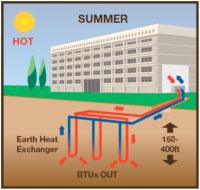
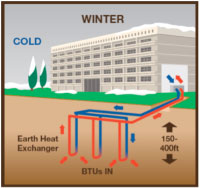
GHP systems consist of three major components: The earth heat exchanger, the heat pump, and the air distribution system.
The earth heat exchanger is what makes these systems so efficient. The heat exchanger is a series of bore holes between 200 and 500 feet deep, connected through a continuous pipe system made of high density polyethylene pipe that snakes in and out of the boreholes and acts much like the radiator in a car. The heat exchanger supplies water to the heat pump.
The heat pump is located inside and takes the place of both the chiller and boiler of a traditional system. A heat pump is very similar to a standard air conditioner except it is more efficient and can heat and cool. The air distribution system is comprised of the air ducts and vents common to all centralized HVAC systems. Radiant floors and ceilings could also be used for distributing and collecting heat.
As you layout your green building strategy, keep in mind that GHP will work with all your active, passive and energy efficiency designs to help reduce the overall cost of wind, solar or other renewable energy options. With the total energy demand reduction, you can dramatically shrink your investment to be put towards other parts of the project. If you are trying to build a Net Zero building, GHP should be the foundation of your plan.
LEED Points for your project
GHP systems reduce energy use so dramatically that they increase your chances of achieving LEED® certification or becoming a Net Zero Energy building. GHPs can earn up to 19 points for the energy optimization credit in the Energy and Atmosphere category of the LEED® rating system. They can also contribute to credits for water conservation and refrigeration management. Some Industry publications estimate GHPs can contribute over 30 points towards LEED® certification.
Utilities can find GHP a useful tool in dealing with demand side management and load reductions. GHP systems are available 24/7/365, unlike solar or wind, don’t require transmission lines and have no geographic or climate limitations. Additionally, GHPs can significantly reduce peak demand, with less need for dirty peak power plants.
Another big advantage for GHP is that the main components of the system are either underground or inside the building, which eliminates vandalism and weathering. The entire system has only two moving parts, the pump and compressor, which makes for easy maintenance, operation and replacement when needed. The underground heat exchanger is made of virtually indestructible high-density polyethylene pipe, which carries a 50 year warranty, and is likely to last far longer than the building it serves.
Lifecycle Cost
It’s not unusual that a GHP system will have a slightly higher upfront cost than traditional HVAC systems, but energy savings, reduced water bills, simplified operation and low maintenance costs lead to quick cost recovery and significantly lower lifecycle costs. Recovering the cost premium can take as little as two years and lead to decades of operating savings. Federal, state, and local government tax incentives, as well as utility energy efficiency grants, can reduce or, in some cases, even eliminate the cost differential between GHP and conventional HVAC.
Another key advantage of GHP systems is their extreme versatility. GHP has been used successfully in the widest extremes, from upstate New York with its frigid winters, to the scorching desert near Las Vegas, and pretty much everything in between. There are GHP systems at the Statue of Liberty Gift Shop, Harvard Library, and the ASHRAE headquarters in Atlanta, GA. GHPs have been most widely used at schools and military facilities. For instance, Ball State University in Indiana is planning a GHP system that will include 8100 boreholes to heat and cool over 50 buildings on campus.
The military, government, and schools were early adopters GHP technology, but now the private sector is catching on. Big box retailers such as Wal-Mart and Ikea are now on the list of GHP supporters.
GHP is very flexible, can be used in any climate and is very cost effective; the one significant limitation is that it requires a significant amount of space to install the geothermal bore field. High rises, with small footprints but large square footage and high energy requirements, may not have sufficient ground surface area. However, buildings with large surface parking areas, gardens, green spaces or plaza areas usually qualify. And it’s possible to build directly on top of the borefield, as well.
Without a doubt, GHP is the most energy efficient HVAC technology on the market today. It cuts energy use, water consumption, and greenhouse gas emissions, all the while saving facility owners money through big costs savings. As the push to develop more green buildings continues to grow, GHP will become one of the most important technologies in the market.
source: Green Building Pro